A failed compressed air test can be a hassle, often leaving companies who thought their compressed air was contaminant free struggling to figure out what went wrong and how to correct the issue. Some of these failures can pose a great risk to one’s health, and even death if gone unnoticed or left unsolved. Considering the costs and stress associated with a failed compressed air test, many breathing air users, providers, and suppliers look to preventative maintenance and monitoring plans.
Once one of the most common reasons for a failed compressed air test, particularly in the SCUBA industry, Carbon Dioxide (CO2) became a less common cause of non-compliance after the Compressed Gas Association raised the limit for their Grade E specification. For example, most sport diving facilities (up to 130 feet) test their compressed air to ANSI/CGA G-7.1 Grade E standard which limits CO2 to 1000 parts per million (ppm).
1. Ambient Air & Intake Location
For those that do fail a test, the reason is often caused by the air that the compressor takes in: the compressor intake. As with other contaminants, if the air your compressor takes in contains high levels of CO2, the air taken into the compressor’s cylinders will also contain high levels of CO2. Carbon dioxide can contaminate a compressor’s intake air for a variety of reasons. For instance, if the intake is in a closed off room (perhaps in winter) that has a large number of people in it exhaling CO2, or if the compressor is in an area near vehicles that are running and emitting exhaust. Thus, intake location plays a role in reported failures. Gross contamination of the intake air will affect the efficiency of the purification filters which could subsequently affect the air quality produced by the compressor.
The best way to determine the quality of the air your compressor is taking in is to test the ambient air around your intake. Because CO2 levels can vary dramatically throughout the day, multiple air samples should be taken at different times of the day if you received a failure for CO2. Air that is taken into the compressor at one time of the day may be within specifications, while at another time of the day it may contain high levels of CO2 due to increased traffic or poor ventilation. Multiple air tests throughout the year and at different times during the day can identify the best time to test and place to run your compressor.
2. Ventilation
Because CO2 is a product of human respiration, reading levels can often increase during the winter when more people are indoors and closed windows lead to poorer ventilation. Harmful fumes, engine exhaust, and welding gases can also be unknowingly trapped in a poorly ventilated area.
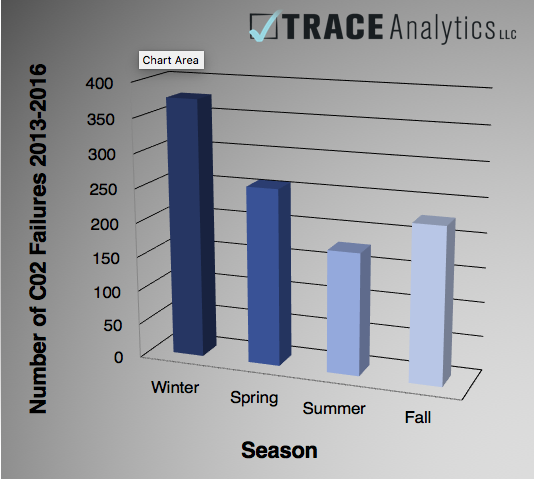
3. The Compressor and Its Filters
Apart from intake air, the compressor itself may be a source of CO2. During the first few hours of operation some compressor filters will remove CO2. But this CO2 will be released into the compressed air once the filter becomes saturated with water, causing CO2 levels to increase. This is why a monitoring plan is crucial to ensuring your filters are regularly maintained to prevent filter degradation.
Other filters will also convert the much more dangerous Carbon Monoxide (CO) to CO2. This is so minute though, that it will not cause a failure.
Is your compressor running too hot? Could it be due to poor ventilation? The life of the filter cartridge is affected by high temperatures and can degrade increasing chances for CO2 contamination. Ultimately, for most compressors, filters simply cannot be relied upon to remove CO2.
4. Other
There are other, less common, reasons for failed tests due to CO2 such as a leak in the compressor’s air line. It is important to be proactive and to understand how the compressor functions and to be aware of the quality of the ambient air that is taken into the compressor. A thorough understanding of your compressor can save you the trouble of a failed test. The goal is not simply to pass a test, but to provide safe quality air at all times.
For more information about compressed breathing air testing click here.