Compressed Air Best Practices Magazine and Trace Analytics LLC clear confusion on compressed air testing within the manufacturing industry in this comprehensive article. Compressed air is used in more than 70 percent of all manufacturing activities, and when compressed air is used in the production of pharmaceuticals, food, beverages, medical devices, and other products, there seems to be confusion on what testing needs to be performed.
What are the Manufacturing Industry Contaminants in Compressed Air?
Compressed Air & Gas Institute (CAGI) cites 10 contaminants that fall within 4 categories:
- Particles (from pipe scale, wear particles and atmospheric dirt)
- Water (liquid, vapor and aerosol)
- Oil (liquid, vapor and aerosol)
- Microorganisms
The international standard ISO 8573-1:2010 is a compressed air quality specification that addresses these very same specific contaminants by providing a range of purity classes for particles, water, and oil. It does not include classes for gases or microorganisms.
Employing a Standard for Compressed Air Testing
ISO 8573 consists of 9 parts in which ISO 8573-1 is most frequently cited. Parts 2 through 9 provide analytical techniques and sampling methods. Many air compressor and filter manufacturers cite ISO 8573-1:2010 purity classes to describe the quality of air that can be produced with their products.
The summary chart below shows purity classes 0 through X for particles, water, and oil. The end user can then select a purity class for each contaminant based on either equipment installed or air quality required for a specific process or product. The contaminants and limits that need to be tested are defined by the compressor system filtration and point-of-use filters that were selected for your manufacturing facility and product line.
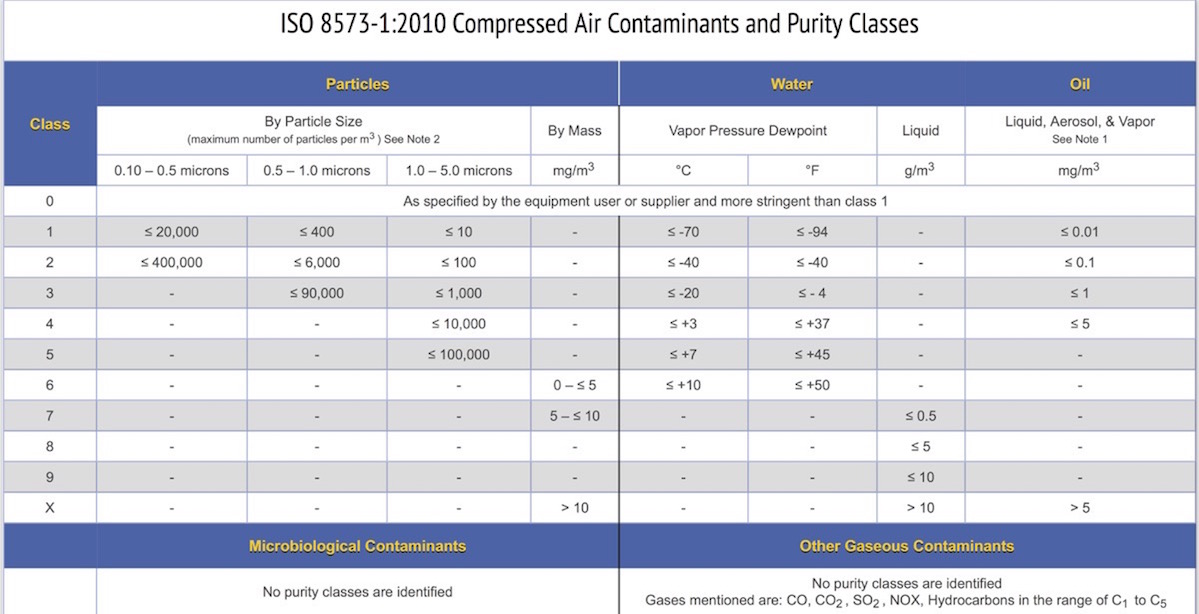
For details regarding microbiological and other gas contaminants in compressed air using ISO 8573 read more here.
Learn How to Designate ISO 8573-1 Purity Classes here.
Is There Any Guidance on Selecting Purity Classes?
Clean, dry air is typically needed by food, beverage, pharmaceutical, and other industries manufacturing a consumable product. There are no mandated air quality specifications, only general statements, such as:
- FDA Code of Regulations Title 21, Part 110.40, Subpart C, Item (g)
- [ICH Q8 (R2) II 4.0]
- Safe Quality Food (SQF) Institute
- BCAS Food and Beverage Grade Compressed Air Best Practice Guideline 102
What Constitutes a Monitoring Program?
- Document the current compressed air system in place.
- Create a diagram of the compressor system, piping and outlets.
- Document air compressor maintenance.
- Perform air quality testing for particles, water, oil, and microorganisms over a period of time to gather sufficient data points for a trend analysis.
- Review trend analysis results.
A) Confirm that air quality is meeting levels specified in corporate quality control documents, or B) Identify over time the appropriate compressed air quality for the product being manufactured so that purity classes can be selected and documented.
How to Sample Compressed Air Quality
Trace Analytics developed the AirCheck Kit™ Model K8573 specifically to address the needs of today’s manufacturer.