Compressed air has a variety of uses in the medical device industry from coating application, to product transfer, to equipment and product cleaning. Because medical devices are placed inside the human body, the products are particularly high-risk. The human body is very sensitive to invasive materials and it is the responsibility of manufacturers to ensure the products that they provide are up to safety standards.
Sanitation and cleanliness are the most important aspects of medical device manufacturing. Since compressed air is a critical factor in the manufacturing of medical devices, this applies to compressed air systems as well. Contaminated compressed air can compromise the integrity of the medical device products and put consumers at risk. Compressed air must meet medical device quality standards and manufacturers have to provide validation that their air systems are clean, effective and pose no risk to consumers.
Contaminants and Consequences
Oil, particulates, water vapor, and bioburden are particularly dangerous compressed air contaminants that can affect medical devices.
Oil-free air is a critical in medical device and pharmaceutical manufacturing (Arfalk, 2016). Cleanroom specifications require that no oil is present at Critical Control Points. Oil can cause some products to increase in size or experience a chemical imbalance (Nortec, 2018). Oil-free air compressors and adequate filtration can help manufacturers prevent and remove oil from the air.
Particulate contamination can affect the safety of medical device products as well. For example, if metal shavings are present in the distribution line and then impact the products, this could not only harm the physical appearance of the product but also put the consumer in danger.
Compressed air is often used to dry medical device products and if that air is contaminated with water vapor, the instruments will not completely dry (Chobin, 2017). This can cause degradation of some products and become a breeding ground for additional contamination like microorganisms.
Bioburden is particularly dangerous and a contamination can threaten patient safety or lead to regulatory intervention. Compressed air systems that are improperly maintained or have inadequate materials can introduce bacteria, yeast, or mold to the end product. This type of contamination puts consumers at a great risk.
Critical Control Points and Safeguards
A medical device compressed air system should include a properly maintained compressor, adequate piping and distribution, and effective filters. It’s essential to properly maintain the system, monitor closely for leaks, and change filters as per the manufacturer’s recommendations. Contaminants can enter the system in a variety of places from the intake, to the piping, to a system leak. Because of this, it is important to consider various points on the system as critical control points and to test as such. For example, testing only at the compressor could allow for contamination down the line to go undetected. Monitoring the air quality in a variety of locations can help manufacturers narrow down a contamination source and act efficiently to correct it.
Preventative maintenance and testing is a good way to safeguard the product and ensure that the system continues to run effectively. Choose the appropriate, particle-free piping, connectors, and hoses, employ effective filtration, and test the systems regularly.
Specifications for Medical Devices
Because there are no specific standards for compressed air in the medical device industry, many manufacturers either work with cleanroom standards or create their own specifications based on a thorough risk assessment. USP (United States Pharmacopeia) and the European Pharmacopoeia standards state the importance of testing for water vapor and oil in medical device products. Oil should not exceed 0.1 mg/m3 (GMP, 2017). There should be no liquid water present.
According to the FDA’s Quality System Regulation requirements, manufacturers must establish and maintain procedures to prevent contamination that could have adverse effects on product quality. Monitoring plans are an effective way to meet these requirements.
A more specific set of standards that can be used for medical devices is ISO 8573. Follow this international standard with purity classes and corresponding specifications for optimal safety.
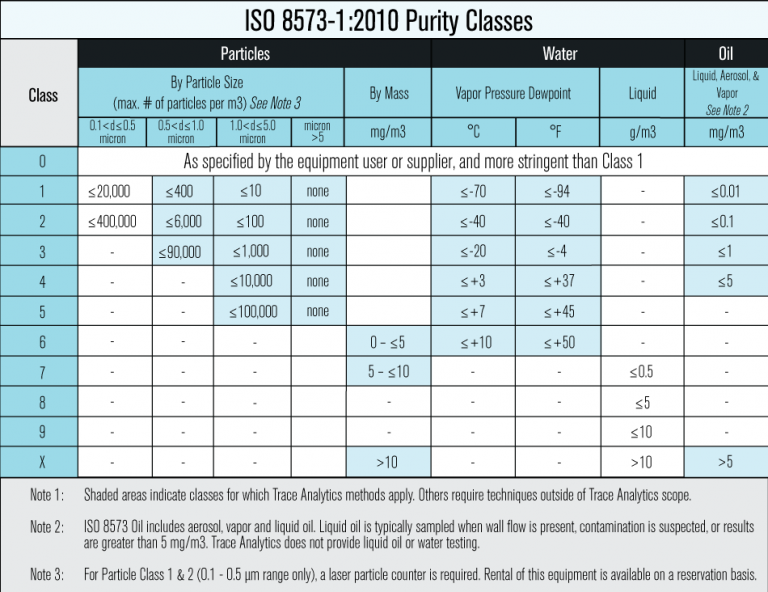
Compressed Air Testing and Monitoring Plans
The best way to ensure compressed air quality used in medical device manufacturing is with regular testing with an accredited laboratory like Trace Analytics, LLC. Diagnostic testing can help to determine current purity levels and provide the necessary data to build a monitoring plan. Testing for particles, water, oil, and microorganisms can be easily and quickly taken care of with a laboratory like Trace. A team of experts, step-by-step instructions and videos and straightforward results allow for peace of mind.
Trace Analytics, LLC can meet any of the above specifications and work with individual specs and needs. Maintain the quality of your compressed air with regular testing.